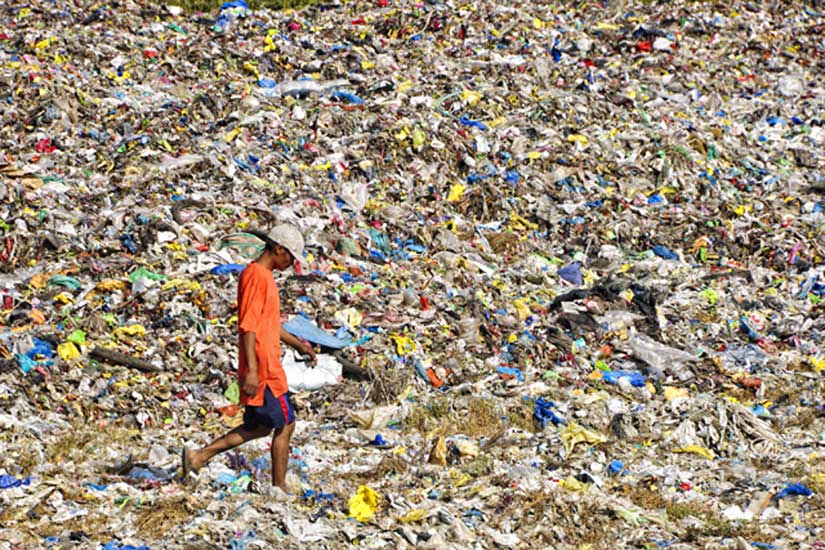
JAKARTA — The global consumer goods industry’s plans for dealing with the vast plastic waste it generates can be seen here in a landfill on the outskirts of Indonesia’s capital, where a swarm of excavators tears into stinking mountains of garbage.
These machines are unearthing rubbish to provide fuel to power a nearby cement plant. Discarded bubble wrap, take-out containers and single-use shopping bags have become one of the fastest-growing sources of energy for the world’s cement industry.
The Indonesian project, funded in part by Unilever PLC, maker of Dove soap and Hellmann’s mayonnaise, is part of a worldwide effort by big multinationals to burn more plastic waste in cement kilns, Reuters has detailed for the first time.
This “fuel” is not only cheap and abundant. It’s the centerpiece of a partnership between consumer products giants and cement companies aimed at burnishing their environmental credentials. They’re promoting this approach as a win-win for a planet choking on plastic waste. Converting plastic to energy, these companies contend, keeps it out of landfills and oceans while allowing cement plants to move away from burning coal, a major contributor to global warming.
Reuters has identified nine collaborations launched over the last two years between various combinations of consumer goods giants and major cement makers. Four leading sources of plastic packaging are involved: The Coca-Cola Company, Unilever, Nestle S.A. and Colgate-Palmolive Company. On the cement side of the deals are four top producers: Switzerland’s Holcim Group, Mexico’s Cemex SAB de CV, PT Solusi Bangun Indonesia Tbk (SBI) and Republic Cement & Building Materials, Inc., a company in the Philippines.
These projects span the world, from Costa Rica to the Philippines, El Salvador to India. In Indonesia, for instance, Unilever is partnering with SBI, one of that country’s largest cement makers.
The alliances come as the cement industry — the source of 7% of the world’s carbon dioxide emissions — faces rising pressure to reduce these greenhouse gases. Consumer brands, meanwhile, are feeling the heat from lawmakers who are banning or taxing single-use plastic packaging and pushing so-called polluter-pays legislation to make producers bear the costs of its clean up.
Critics say there’s little green about burning plastic, which is derived from oil, to make cement. A dozen sources with direct knowledge of the practice, among them scientists, academics and environmentalists, told Reuters that plastic burned in cement kilns emits harmful air emissions and amounts to swapping one dirty fuel for another.
More importantly, environmental groups say, it’s a strategy that could potentially undercut efforts spreading globally to boost recycling rates and dramatically slash the production of single-use plastic.
Such thinking is naive, said Axel Pieters, chief executive of Geocycle, the waste-management arm of Holcim Group, one of the world’s largest cement makers and partner with Nestle, Unilever and Coca-Cola in plastic-fuel ventures. Mr. Pieters told Reuters that burning plastic in cement kilns is a safe, inexpensive and practical solution that can dispose of huge volumes of this trash quickly. Less than 10% of all the plastic ever made has been recycled, in large part because it’s too costly to collect and sort. Plastic production, meanwhile, is projected to double within 20 years.
“Thinking that we recycle waste only, and that we should avoid plastic waste, then you can quote me on this: People believe in fairy tales,” Mr. Pieters said.
Unilever would not comment specifically on the Indonesia project. It said in an e-mail that in situations where recycling isn’t feasible, it would explore “energy recovery initiatives.” That’s industry parlance for burning plastic as fuel.
Coca-Cola, Unilever, Colgate, and Nestle did not respond to questions about the environmental and health impacts of burning plastic in cement kilns. The companies said they invest in various initiatives to reduce waste, including boosting recycled content in their packaging and making refillable containers.
Cemex, SBI, Republic Cement and Holcim’s Geocycle unit told Reuters their partnerships with consumer goods firms were aimed at addressing the global waste crisis and reducing their dependence on traditional fossil fuels.
Exactly how much plastic waste is being burned in cement kilns globally isn’t known. That’s because industry statistics typically lump it into a wider category called “alternative fuel” that comprises other garbage, such as scrap wood, old vehicle tires and clothing.
The use of alternative fuel has risen steadily in recent decades and already is the dominant energy source for the cement industry in some European countries. There’s no question the amount of plastic within that category has increased and will keep climbing given a worldwide explosion of plastic waste, according to 20 cement industry players interviewed for this report, including company executives, engineers and analysts. Reuters also reviewed data from cement associations, individual countries and analysts that confirmed this trend.
For example, Geocycle currently uses 2 million tonnes of plastic waste a year as alternative fuel at Holcim plants worldwide, according to Geocycle CEO Mr. Pieters, who said the company intends to increase this to 11 million tonnes by 2040, including through more partnerships with consumer goods companies.
Pieters said the cement industry has the capacity to burn all the plastic waste the world currently produces. The United Nations Environment Programme estimates that figure to be 300 million tonnes annually. That dwarfs the world’s plastic recycling capacity, estimated to be 46 million tonnes a year, according to a 2018 estimate by the Organisation for Economic Co-operation and Development (OECD), a global policy forum.
Plastic pollution, meanwhile, is bedeviling communities whose landfills are reaching capacity and despoiling the Earth’s wild places. Plastic garbage flowing into the oceans is due to triple to 29 million tonnes a year by 2040, according to a study published last year by the Pew Charitable Trusts. This detritus is endangering wildlife and contaminating the seafood humans consume.
“The cement industry is definitely a solution,” Geocycle’s Mr. Pieters said.
TOXIC EMISSIONS
Consumer goods giants are turning to cement firms for help in reducing plastic litter as other initiatives stumble. Reuters reported in July that a set of new “advanced” plastic recycling technologies promoted by big brands and the plastic industry had suffered major setbacks across the world.
Cement-making is one of the world’s most energy-intensive businesses. Fuel – mainly coal – is its single-biggest expense, industry executives said. In the 1970s, producers looking to reduce costs began stoking kilns with rubbish such as tires, biomass, sewage sludge – and plastic. Those materials aren’t as efficient as coal, but are virtually free. Some local governments even pay cement makers to take this waste.
In Europe, refuse now makes up roughly half the fuel used by the cement industry. In Germany, the bloc’s biggest producer, the ratio is 70%, according to 2019 data from the Global Cement & Concrete Association (GCCA), a London-based trade organization. The United States uses 15% alternative fuel in its kilns, according to the Portland Cement Association, a US industry group. Spokesperson Mike Zande said its members have the capacity to catch up with Europe.
While cost-cutting remains the primary driver, the industry in recent years has begun touting its garbage fuel as a way to reduce the “societal problem” of plastic waste, said Ian Riley, CEO of the London-based World Cement Association (WCA), which represents producers in developing countries.
So it was logical that cement makers would team up with consumer goods companies, the largest source of single-use plastic packaging, in the recent partnerships to burn discarded plastic in their kilns.
In emerging markets, big brands sell a slew of food and hygiene products packaged in plastic sachets, typically single-serving portions tailored to the budgets of poor households. Billions of these flexible pouches are sold each year. Sachets are nearly impossible to recycle because they’re made of layers of different materials laminated together, usually plastic and aluminum, that are difficult to separate.
Indonesia, an archipelago of more than 270 million people, is the second-largest contributor to ocean plastic pollution behind China, partly due to its widespread use of sachets, according to a 2015 study published in the journal Science. Plastic garbage can be seen everywhere around Jakarta, the sprawling capital of more than 10 million people. It clogs storm drains, litters its teaming slums and mars its shoreline.
Developing countries have generally welcomed assistance with waste management. Thus Indonesia was a natural location for Unilever’s waste-fuel venture with cement maker SBI and the local Jakarta government. At last year’s launch, Andono Warih, head of Jakarta’s environment service, praised the initiative and expressed hope that it would spark other such collaborations.
The project uses plastic that’s already been buried in the region’s Bantar Gebang landfill, one of the largest dumps in Asia. Waste excavated by earth-moving equipment is transported to a warehouse at the landfill site. There, it is shredded, sieved and dried into a brown mix resembling manure. That material, known as Refuse Derived Fuel (RDF), is then fed into the kiln at an SBI cement plant in Narogong, just outside Jakarta.
SBI currently uses 20% RDF at that plant, a figure that could increase to 35%, according to Ita Sadono, SBI’s business development manager. The operation still relies primarily on coal, she said, but she contends RDF is “significantly helping to reduce plastic waste.”
Unilever is helping to fund a second RDF project in Cilacap, an industrial region in Central Java, according to SBI and a 2020 sustainability report by Unilever’s local Indonesian unit. The two facilities could send 30,000 tonnes of plastic waste per year to SBI’s cement plants, according to a Reuters analysis of data provided by SBI.
Unilever did not respond to detailed questions about these projects. Ms. Sadono said in a text message that Reuters’ calculations were “OK,” without giving further details.
About two kilometers from SBI’s cement plant near Jakarta, Dadan bin Anton, 63, runs a roadside stall selling plastic sachets of soap, washing powder and instant coffee, including brands owned by Unilever. He said he often has trouble breathing and blames the cement plant.
“People here are breathing dust every day,” he said.
SBI has invested in mitigation measures to cut dust at its plants, Sadono said. And it isn’t clear whether the cement facility has anything to do with Mr. Dadan’s burning chest. Jakarta boasts some of the dirtiest air in Asia. Pollutants from industry smokestacks, agricultural fires and auto exhaust routinely blanket the city.
But some scientists say incinerated plastic is a dangerous new ingredient to add to the mix, particularly in developing nations where air-quality rules often are weak and enforcement spotty.
Plastic releases harmful substances like dioxins and furans when burned, said Paul Connett, a retired professor of environmental chemistry and toxicology at St. Lawrence University in Canton, New York, who has studied the poisonous byproducts of burning waste. If enough of those pollutants escape from a cement kiln, they can be hazardous for humans and animals in the surrounding area, Mr. Connett said.
Such fears are overblown, said Claude Lorea, cement director at GCCA, the industry group representing big cement firms including Holcim and Cemex. She said super-heated kilns destroy all toxins resulting from burning any alternative fuel, including plastic and hazardous waste.
But things can go wrong.
In 2014, a cement plant in Austria released hexachlorobenzene (HCB), a highly toxic substance and suspected human carcinogen, after the facility burned industrial waste contaminated with the pollutant. Cheese and milk sourced from cattle raised near that plant in southern Carinthia state were tainted, Austria’s health and food safety agency found. And blood samples drawn from area residents also contained HCB, which can damage the nervous system, liver and thyroid.
An investigation commissioned by the state government found multiple failures by local regulators and the cement plant, including that the kiln was not running hot enough to destroy contaminants like HCB.
The Austrian cement maker which operates the plant, w&p Zement GmbH, told Reuters that it had worked to eliminate all the environmental pollution from the incident and that it had provided help to the community such as replacing contaminated animal feed.
Carinthia province spokesperson Gerd Kurath said in an email that the government’s continued monitoring of air, soil, and water samples in the area shows that contamination levels have declined.
The cement industry, meanwhile, is heralding waste-to-fuel as a way to fight global warming. That’s because burning refuse, including plastic, emits fewer greenhouse gases than coal, the GCCA trade group said.
Burning garbage “reduces our fossil fuel reliance,” spokesperson Lorea said. “It’s climate neutral.”
The European Commission, which sets emission rules in Europe, told Reuters that plastic does emit fewer carbon dioxide emissions than coal but more than natural gas, another fuel used by the cement industry.
The US Environmental Protection Agency, which regulates environmental policy in the world’s largest economy, reached a different conclusion. It said in a statement there is no significant climate benefit to be gained from substituting plastic for coal, and that burning this waste in cement kilns can create harmful air pollution that must be monitored.
Measuring plastic’s CO2 emissions against those of coal, the world’s dirtiest fossil fuel, is not the benchmark to use if the cement industry is serious about fighting global warming, said Lee Bell, advisor to the International Pollutants Elimination Network, a global coalition working to eliminate toxic pollutants. Reducing the industry’s massive carbon emissions, he said, requires a switch to fuels such as green hydrogen, a more expensive but low-polluting fuel produced from water and renewable energy.
“The cement industry should leap-frog the whole burning-waste paradigm and move to clean fuel,” Mr. Bell said.
The GCCA told Reuters the industry is improving energy efficiency and is considering the use of green hydrogen.
EVER MORE PLASTIC
While cement plants in industrialized countries are gearing up to burn more plastic, explosive growth is anticipated in the developing world.
China and India together account for 60% of the world’s cement production in facilities whose primary fuel is coal. Over the next decade, these countries have set targets of using alternative fuel to stoke 20% to 30% of their output. If they reached just a 10% threshold, that would equate to burning 63 million tonnes of plastic annually, up from 6 million tonnes now, according to SINTEF, a Norwegian scientific research group. That’s more plastic waste than the United States generates each year.
In 2019, 170 countries agreed to “significantly reduce” their use of plastic by 2030 as part of a United Nations resolution. But that measure is non-binding, and a proposed ban on single-use plastic by 2025 was opposed by several member states, including the United States.
Thus the waste-to-fuel option may well become an unstoppable juggernaut, said Matthias Mersmann, chief technology officer at KHD Humboldt Wedag International AG, a German engineering firm that supplies equipment to cement plants worldwide.
Plastic waste is quickly outstripping countries’ capacity to bury or recycle it. Burning it eliminates large amounts of this material quickly, with little special handling or new facilities required. There are an estimated 3,000 or more cement plants worldwide. All are hungry for fuel.
“There’s only one thing that can hold up and break this trend, and that would be a very strong cut in the production of plastics,” Mr. Mersmann said. “Otherwise, there is nothing that can stop this.”
That momentum has some environmentalists worried, including Sander Defruyt, who heads a plastics initiative at the Ellen MacArthur Foundation, a United Kingdom-based nonprofit focused on sustainability. The foundation in 2018 worked out waste-reduction and recycling targets with Coca-Cola, Nestle, Unilever, Colgate-Palmolive and hundreds of other consumer brands.
Mr. Defruyt said the foundation does not support its partner companies’ pivot towards incineration. Burning plastic for cement fuel, he said, is a “quick fix” that risks giving consumer goods companies the green light to continue cranking out single-use plastic and could reduce the urgency to redesign packaging.
“If you can dump everything in a cement kiln, then why would you still care about the problem?” Mr. Defruyt said.
Coca-Cola, Nestle, Unilever, and Colgate-Palmolive said their cement partnerships are just one of several strategies they’re pursuing to address the waste crisis.
‘PLASTIC PRAYERS’
In the central England village of Cauldon, residents have complained in recent years to the local council and Britain’s environmental regulator about noise, dust and smoke coming from a nearby cement plant owned by Holcim. Those efforts have failed to derail the expansion of that facility to burn more plastic.
When completed next year, alternative fuel, including “non-recyclable” plastics such as potato chip bags, will account for up to 85% of the facility’s fuel, according to planning documents filed with local authorities on behalf of Geocycle, which will manage the project.
The move will recover energy from plastic waste otherwise destined for landfills, the documents said.
Cauldon resident Lucy Ford, 42, said the cement maker’s plans have only added to some villagers’ fears about emissions. “They say they are the answer to all of our plastic prayers,” she said. “I don’t like the idea of it.”
Geocycle’s Mr. Pieters said he understood the community’s concerns. He said the company complies with all local regulations and that it carefully monitors the plant’s emissions, which would be lowered by the upgrades.
Britain’s Environment Agency said in an e-mail that it took all complaints about the plant seriously. It said the Cauldon facility has a permit to burn waste and that the plant has to comply with its regulations.
Back in Indonesia, Unilever and SBI told Reuters that using plastic for energy was preferable to leaving it in a landfill.
Local environmentalists say they are alarmed that cement kilns could be shaping up as the fix for a nation flooded with plastic waste.
It would allow consumer brands to continue business as usual, while adding to Indonesia’s air-quality woes, said Yobel Novian Putra, an advocate with the Global Alliance for Incinerator Alternatives, a coalition of groups working to eliminate waste.
“It’s like moving the landfill from the ground to the sky,” Mr. Putra said. — Joe Brock, Yuddy Cahya Budiman, John Geddie and Valerie Volcovici/Reuters